Converting animal and plant waste into energy can be a triple-hitter: It not only helps reduce waste going to landfills or from being released as gas into the atmosphere, but saves energy and money. Waste materials – ranging from animal manure for methane to wood chips for direct heat to waste vegetable oil for straight use or conversion to biodiesel – also have a positive energy and carbon balance. That is, more energy is derived from the fuel than is spent converting it. Therefore, no net CO2 is generated.
Animal Manure
Nature has always used anaerobic digestion – bacteria breaking down organic material in the absence of oxygen – to recycle waste. Modern anaerobic digester systems on livestock farms work on the same principle: The solids in manure are converted by bacteria into biogas, primarily methane, which can then be used to generate electricity.
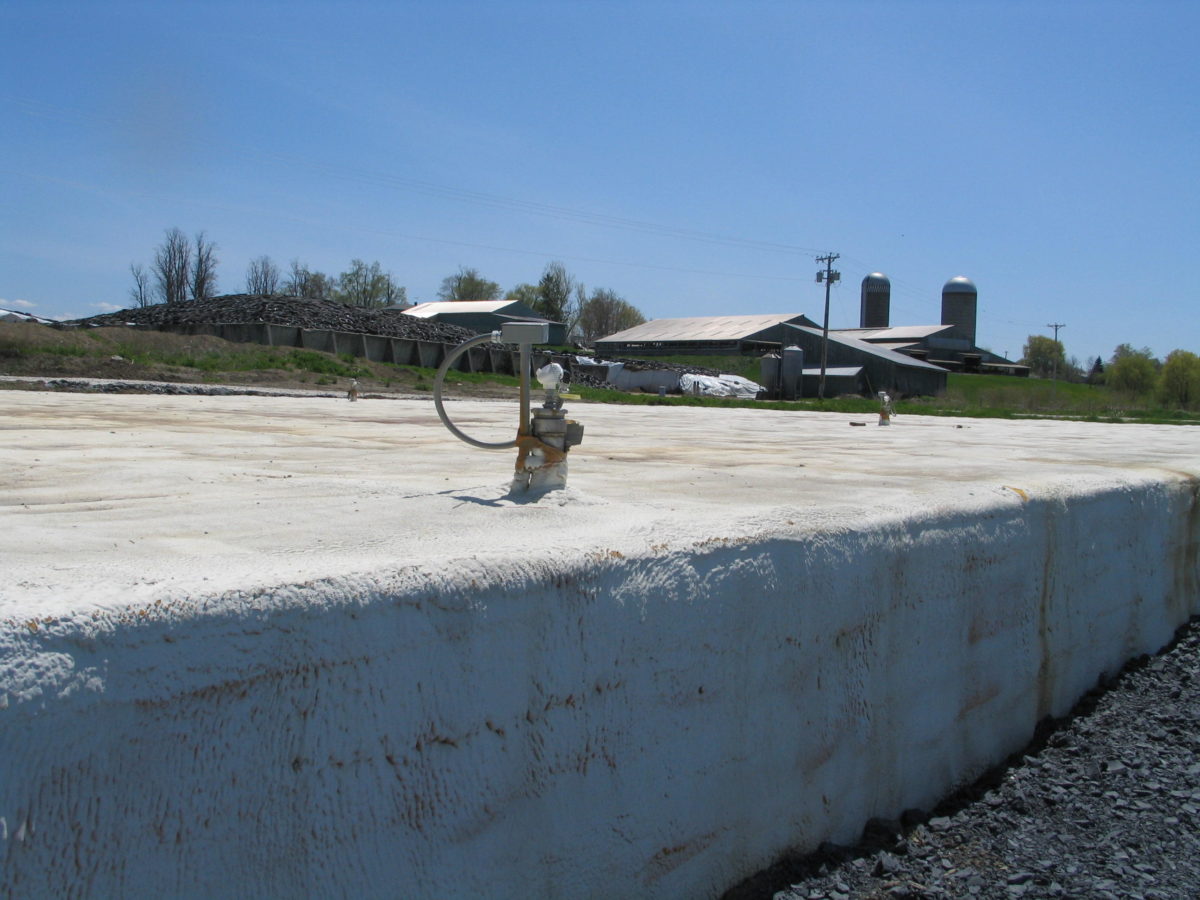
Anaerobic digesters have traditionally been geared toward large livestock confinement operations, which produce a lot of manure. The digester’s broader-use potential, however, has spurred manufacturers to explore scaling down the technology for small- and mid-sized farms. China and India have long promoted smaller digesters. And nearly 2,000 farm-based digesters operate in Europe, where researchers are trying to improve efficiency and cost-effectiveness for smaller operators by combining food and animal waste.
Digesters resolve multiple problems simultaneously:
- When the liquids and solids are separated and treated, odor is reduced. The liquid portion is much easier to apply as fertilizer and is often mixed directly with irrigation water.
- The odor- and pathogen-free solids can be sold as compost or reused as bedding, either generating new revenue streams or saving producers money on purchased bedding.
- Fly populations in and around the manure storage systems are reduced, as are weed seed populations in the compost.
- Biogas is captured and burned to power the farm and/or generate electricity to be sold back to the power supplier. Capturing and using the methane prevents its discharge to the atmosphere, where it has 21 times more global warming potential than CO2.
In 1998, AgSTAR, a collaborative effort of various federal agencies, selected the 1,000-acre, four-generation Haubenschild family farm near Princeton, Minn., to demonstrate the effectiveness of an on-farm digester operation. The Haubenschild’s digester receives, on average, 20,000 gallons of manure per day, producing 72,500 cubic feet of biogas, most of which is used to power a 135 kW generator. Waste heat recovered from the generator’s cooling jacket is used to heat the barn. As an added benefit, the Haubenschilds are able to supply enough electricity for an additional 70 households, and by December 2005, the farm had generated a total of 5.8 million kWh.
The energy produced by the digester prevents the equivalent of burning 50 tons of coal per month. Because it reduces methane release, the Haubenschild Farm can sell 90–100 tons of carbon credits per week through the Environmental Credit Corporation. The farm has also saved an estimated $40,000 in fertilizer costs because they use resulting “digestate” as a soil amendment.
The Haubenschilds are committed to conserving resources and saving money in other ways as well. For example, they reuse milk cooling water for cow drinking water and to wash the floor, then reuse this water for the digester. They also use four tons of recycled newspaper per week as bedding because it promotes excellent anaerobic breakdown of manure.
While promising, digester technology is still evolving, and installation and operating costs are high. Digesters are very sensitive to temperature, alkalinity, loading rate of waste and hydraulic retention time. They require consistent oversight by at least one person. Other challenges include high capital costs, low wholesale electricity prices, still-emerging industry support and hooking up to the grid. (For more information, see Working with Rural Utilities: What’s the Buzz?).
A unique partnership between an investor-owned utility and several Vermont farms is making “cow power” more feasible for a number of growers by allowing customers to choose sustainable energy. Thousands of Central Vermont Public Service (CVPS) customers have signed up to get a portion of their energy through the CVPS Cow Power program. They pay an additional 4 cents per kWh knowing that 100 percent of the premium supports Vermont dairy farmers who use digesters.
It currently takes about 500 milking cows to produce enough energy for Cow Power to be economically viable, so a number of small-scale farms are considering combining their manure to become eligible.
Plant Waste
Fuel made from plant waste is made primarily from either waste vegetable oil (WVO) or WVO converted into biodiesel, a diesel fuel made either partially or wholly from biological materials. With a few exceptions, WVO requires modifying existing equipment, while WVO converted into biodiesel can be used in most diesel-burning engines.
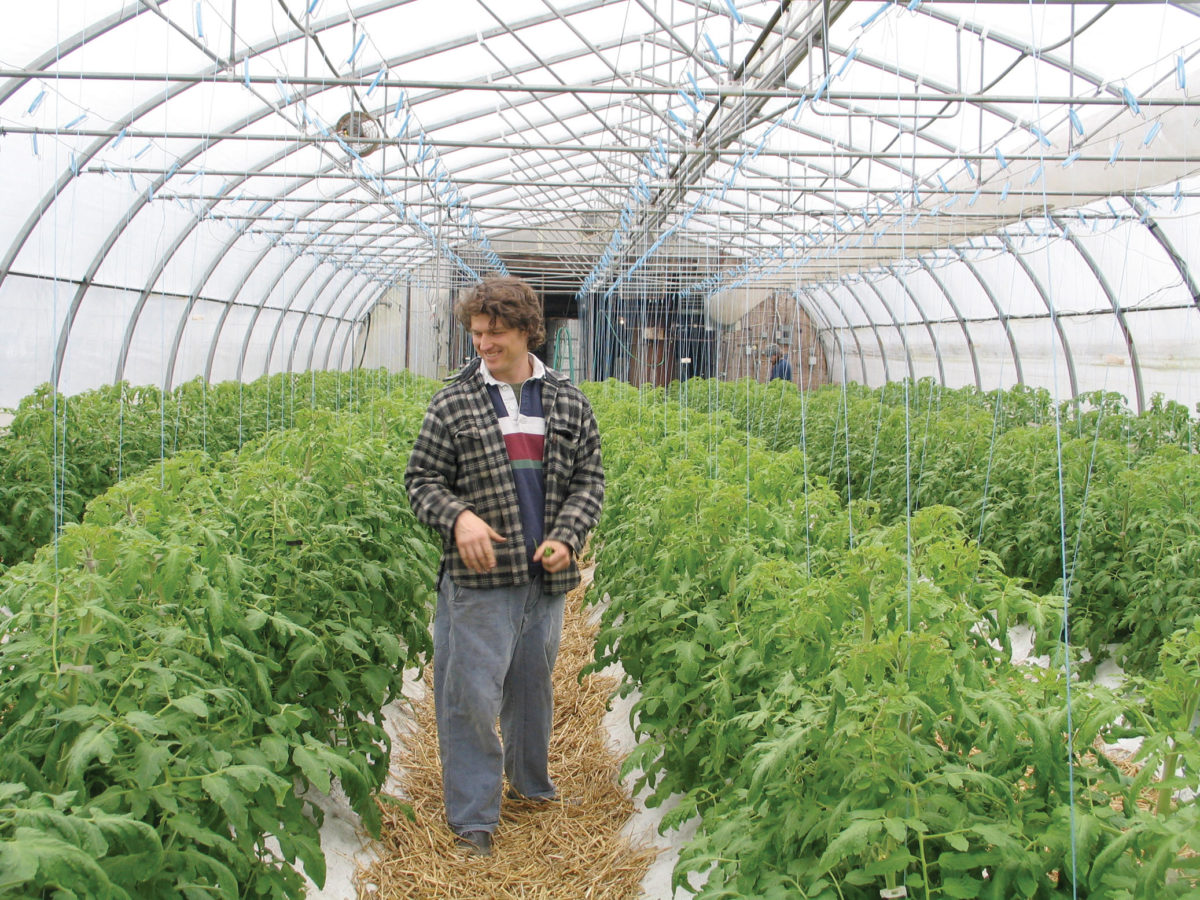
Fuel from waste or converted vegetable oil has pros and cons, but both confer many environmental and economic benefits. Used oil contains nearly twice the energy value of coal and more energy than No. 2 fuel oil. Compared to petroleum diesel, biodiesel produces fewer volatile organic compounds (VOCs) and particulates and less CO2, sulfur dioxide, carbon monoxide and mercury. Some studies suggest that biodiesel produces slightly higher levels of nitrogen oxide (NOx) pollution, but researchers are investigating new additives and diesel technology that could significantly lower these emissions.
Mike Collins and Rebecca Nixon of Old Athens Farm in southeastern Vermont decided to switch to straight waste-vegetable oil to heat their three greenhouses after using as much as 3,000 gallons of No. 2 oil in one winter. Each greenhouse now has a waste oil burner, generating 350,000 BTU for 3,200 square feet.
Collins and Nixon, who grow organic vegetables and berries for direct markets on two acres, and produce greenhouse tomatoes, cucumbers and eggplants, collect waste oil from nearby restaurants. The restaurants are within normal vegetable delivery routes, saving transport-related time and energy. Collins and Nixon avoid oil with hydrogenated fats as it does not perform well in waste oil burners.
The oil, generally kept in containers ranging from five to 50 gallons, is brought to the farm, filtered through a screen and then stored in large plastic tanks in the greenhouse. Because it solidifies in cold weather, any oil kept outside in the winter must be pre-warmed before use.
Like all new energy systems, a vegetable oil system requires initial start-up costs. For Collins and Nixon, each burner cost about $5,000 and another $500 to set up. About four hours per week are required to collect the oil, and to maintain the heaters. Assuming labor costs of $10 per hour, their waste vegetable oil system costs them an additional $2,000 annually in labor.
But the payback is quick. Eliminating expensive fuel purchases meant that during the 2005–2006 growing season, the farm saved almost $7,000 in fuel costs. With heating oil prices just above $2.25 per gallon, payback on this system could be as fast as three and a half years.
Like straight vegetable oil, converting WVO to biodiesel can be cost effective: less than $1 per gallon in materials, plus labor. Matt Steiman, biodiesel project supervisor at Dickinson College in Carlisle, Pa., has long-promoted its benefits. In 2005, on behalf of Wilson College, he received a SARE grant to teach farmers to convert vegetable oil into biodiesel, holding six hands-on workshops and attracting more than 100 growers from Maryland, Virginia, West Virginia and Pennsylvania. Several participants are now receiving seed money to produce biodiesel on their own farms.