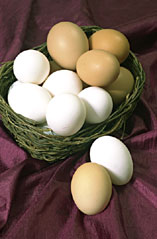
Cooperators on this project reported cost savings associated with reduced pesticide use for fly control, removal of less material from the buildings at cleanout, and the production of a higher value and saleable product. Additional costs were incurred for turning the compost. Based on partial budget analysis including these costs, annual savings equaled $6,000 per building per year. Total annual savings at a 330,000 laying hen facility was approximately $30,000. This was equivalent to a 65% reduction in costs associated with pesticides and manure removal and disposal. Overall, the greatest cost reduction was realized from reducing the amount of pesticide used. The savings offset the costs of new compost turners and other equipment required for in-house composting in less than three years. Additional opportunities were created to use waste cardboard and egg shells from a cracking operation as a carbon source and amendment, respectively, to the compost.