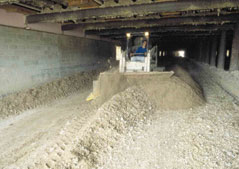
High-rise, Caged Layer Facilities
The standard structure design for high-rise, caged layer facilities involves housing poultry in offset-stacked cages in the upper floor of the structure. Manure from the cages is directed with plastic sheeting into the storage area below (Figure 1). Manure may accumulate for several months or more before buildings are cleaned out.
Automated fans housed in the lower portion of the structure control ambient temperatures in the cage area by drawing air in through evaporative cooling screens located in the roof and expelling it through the walls in the manure storage area. The fans also serve to vent ammonia and other gasses from the building, and to accelerate manure drying. Fly control is normally achieved by supplying a feed-based larvicide to laying hens coupled with topical applications of insecticides on the manure as needed to control outbreaks. Odor and fly complaints are commonly associated with the clean-out process when accumulated manure is disturbed for loading and transport.
An Overview of In-House Composting
Composting is possible inside high-rise facilities using equipment sized to fit in the manure accumulation area of the structure. Cooperators at the sites where this SARE research was conducted used a Brown Bear model 24C compost turner [2] fitted to a skid-steer drive unit to aerate the materials (Photo A). The skid-steer is the same power unit that, when fitted with a loader bucket, is used to remove material from the buildings. To prepare for a compost cycle, a carbon source such as straw or sawdust is spread on the floor after cleaning out a building. Manure is allowed to accumulate on the carbon bed for 2 to 4 days before forming the material into windrows with the turner. The material is turned (aerated) every two to four days, depending on the size of windrows and material temperature.
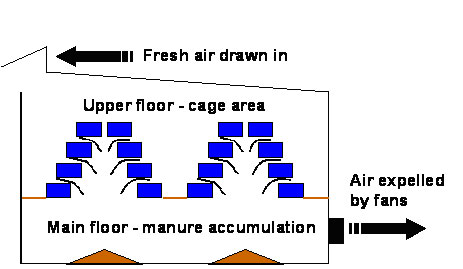
Aerating promotes rapid decomposition by microorganisms. The metabolic heat produced by the microorganisms is capable of generating temperatures in the compost above the lethal limit for fly larvae (110o F). Aerating also rotates fresh manure into the center of the pile where high temperatures kill new fly larvae. Material is removed when the volume exceeds the operational capacity of the turner.
In-house composting differs from traditional composting. Since manure is being added continuously, the product at the end of a cycle is not finished compost. However, as a result of frequent mixing and partial decomposition, the material is more uniform and has a lower moisture content and less odor than fresh poultry manure. If desired, finishing can occur outdoors in a conventional composting system, or partially composted material can be land-applied without finishing. Practitioners should check with state and local officials regarding regulations on composting facilities and compost quality standards before marketing the products of this process as compost.
An essential component of in-house composting is the negative pressure ventilation system that vents ammonia and other gasses from the composting area. This reduces the exposure of poultry and employees to potentially toxic gasses produced during composting. High concentrations of harmful gasses may still be present in the composting area, so employees working there should be equipped with appropriate monitoring and respiratory safety devices. Also, practitioners should be aware of impending air quality rules designed to regulate ammonia emissions from poultry farms. Careful attention to composting conditions, particularly the carbon to nitrogen (C:N) ratio of the material, can limit ammonia emissions. There is also some evidence (cited later) that chemical amendments can be used to reduce ammonia volatilized from composting manure.